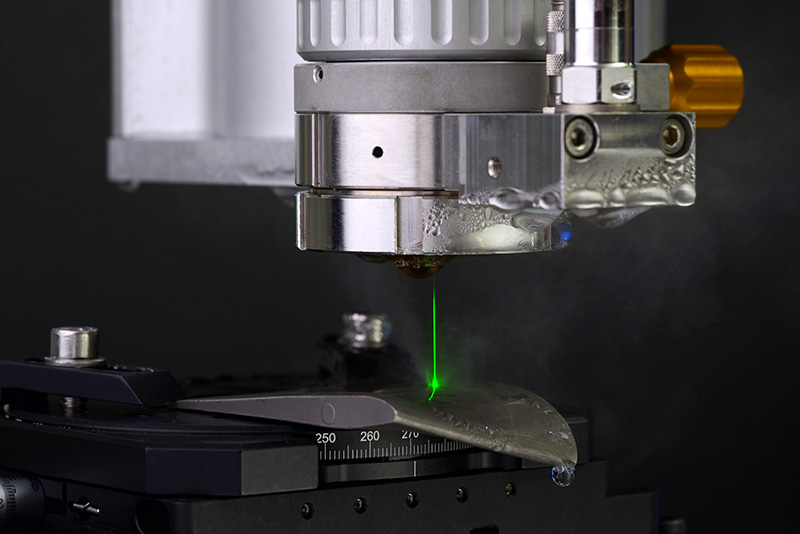
Laser processing systems are becoming increasingly important in the industrial production of micro and macro components for various industries and applications and are thus establishing themselves as an important tool for production. Their technical characteristics such as high precision, reliability, material diversity and the low thermal load on the components contribute to this development, as does the good automation capability of the laser process.
The required low component tolerances and short cycle times, however, present laser processing with ever new challenges. The stability of the process plays a major role here: since laser processes are influenced by various machine-, workpiece- and environment-related factors, even small parameter changes can mean that the components produced are no longer within the intended tolerances. Especially in the production of precision components, the process window, i.e. the range of permissible parameter deviations, is extremely narrow. Therefore, thorough monitoring and precise control of the process is essential in laser micromachining.
Our solution
Here Fraunhofer IPT relies on measurement systems based on short-coherent interferometry, camera- and diode-based measurement of process emission, laser triangulation and chromatic confocal distance measurement. Integrated into the laser processing units, they provide direct process monitoring. The measurement systems can use the same beam path of the laser beam or be introduced with an offset or angle. In this way, the modular inline measurement systems can analyze the component before, during and after processing, depending on the measurement principle. These solutions allow accurate, robust monitoring and control of laser processes that can handle even complex tasks.
Our services
- Development of measurement systems and demand-oriented measurement software
- Project management, requirements analysis, design and implementation
- Integration into manufacturing
- Validation and characterization