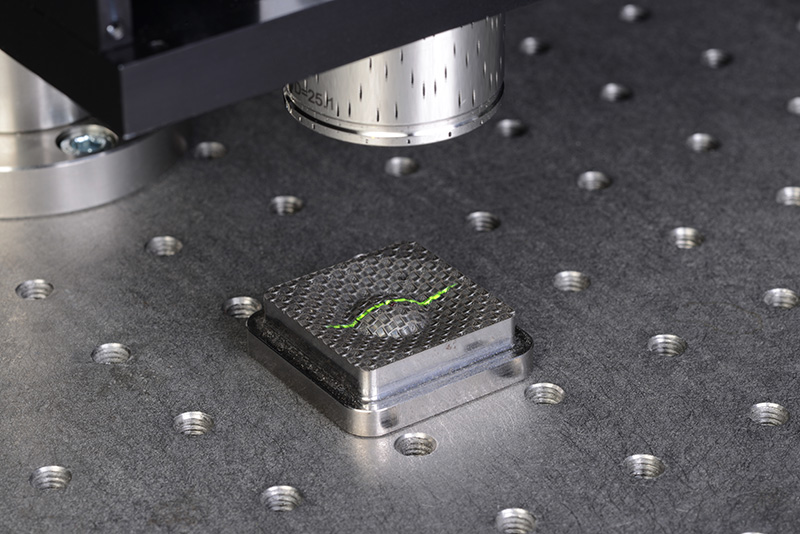
Laser processing systems are increasingly establishing themselves as important tools for production in the industrial manufacturing of micro and macro components. Particularly in the manufacturing of microstructures, the laser can fully exploit its technical advantages such as its high precision and reliability, the variety of materials that can be processed, the extremely low thermal load on the components and the good automation capability
However, with low component tolerances and short cycle times, especially in high-precision applications in the field of ultra-short pulse lasers, laser processing often reaches its limits. Particularly in the manufacturing of precision components, even small changes in process parameters can result in the components produced no longer being within the specified tolerances. Thorough monitoring and precise control of the process is therefore indispensable.
For monitoring laser processes, the Fraunhofer IPT has developed a sensor system based on low-coherence interferometry that can be easily integrated into existing laser processing units. The light beam of the measurment system uses the same beam path that is used for the actual laser beam guidance. In this way, the modular inline measuring system can measure the component before, during and after processing. The measuring module offers high-resolution and submicrometric-accurate dimensional characterization of the surface geometries and is also capable of producing tomographic images of semi-transparent materials. In addition, low-coherence interferometry allows material and surface independent monitoring and adaption of the laser process.
Our services
- Development of measurement systems and demand-oriented signal processing as well as feedback algorithms
- Integration of the measuring systems into existing machines
- Implementation of adaptive process control
- Validation and characterization of the measurement process