Digitales Koordinatenmessgerät und Analysesoftware zur Bauteilprüfung in der 5-Achs-Fräsbearbeitung
Die Qualitätssicherung sicherheitskritischer Bauteile, wie sie in der Luft- und Raumfahrt oder in der Medizintechnik eingesetzt werden, ist aufwändig und erfordert den Einsatz kostspieliger Prüfmaschinen und Messinstrumente. Das Fraunhofer-Institut für Produktionstechnologie IPT in Aachen hat erstmals gemeinsam mit Industriepartnern einen digitalen Zwilling entwickelt, mit dem eine virtuelle Bauteilprüfung basierend auf Prozessdaten möglich ist. Das reduziert Zeit und Kosten für die physische Bauteilprüfung ganz erheblich.
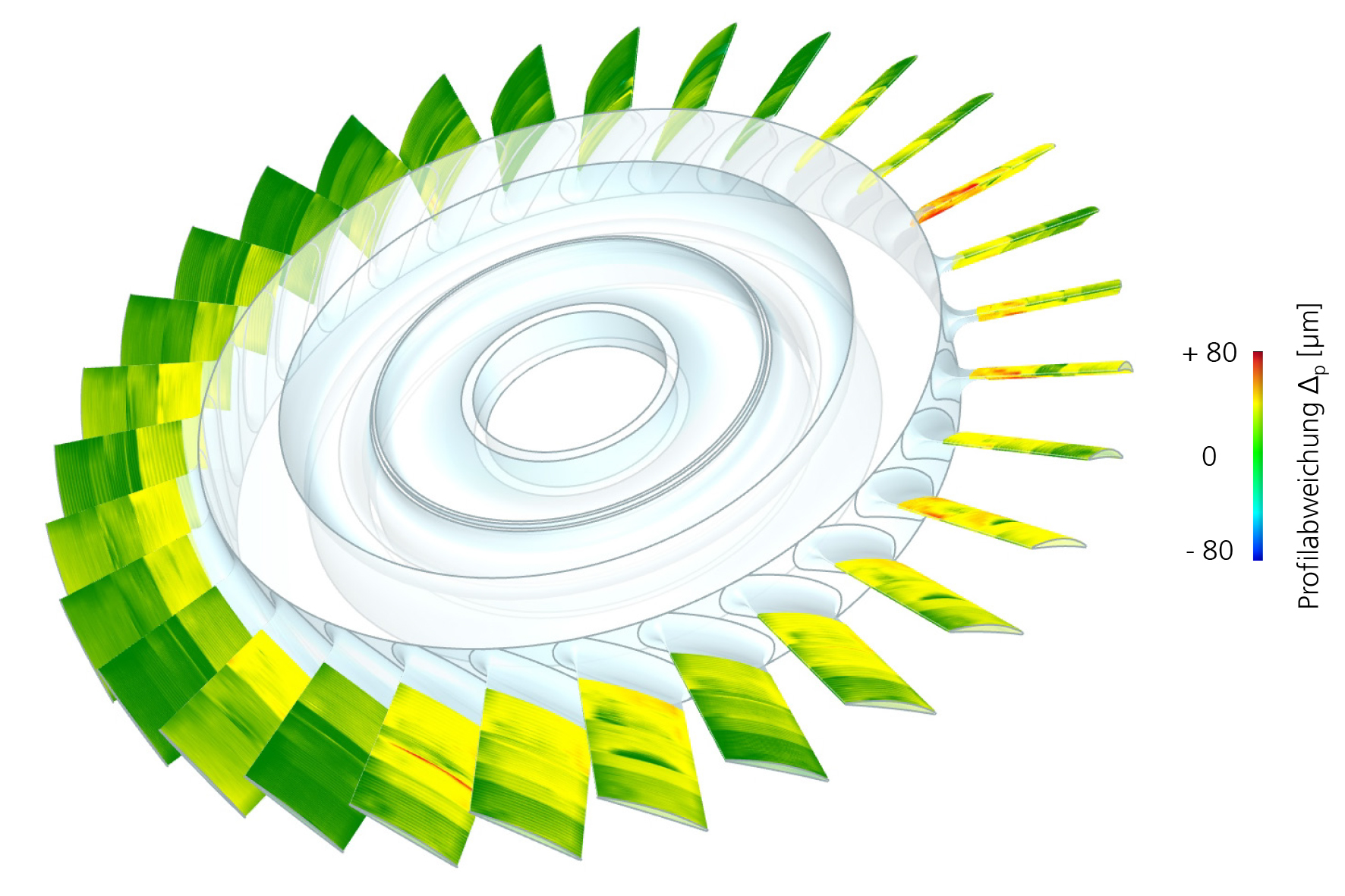
Je nach Anwendungsgebiet und Komplexität des Bauteils entfallen bis zu 25 Prozent der Produktionskosten und 20 Prozent der Durchlaufzeit auf die Prüfung der Bauteilqualität. Eingesetzt werden dafür sowohl optische als auch taktile Messverfahren. Die Digitalisierung von Fertigungsprozessen und die Erfassung und Verarbeitung von Produktionsdaten können dazu beitragen.
Im kürzlich abgeschlossenen Forschungsprojekt »DigitalCMM – Digital Coordinate Measurement Machine« entwickelte ein Forschungsteam des Fraunhofer IPT gemeinsam mit Industriepartnern einen digitalen Zwilling, mit dem sie unmittelbar nach der Fräsbearbeitung ohne zusätzlichen physischen Messaufwand die Qualität des Bauteils bestimmen können.
Koordinatenmessgerät und Analysesoftware zur Vorhersage der Bauteilqualität
Um den digitalen Zwilling zur Qualitätsbestimmung zu erstellen, entwickelten die Forscherinnen und Forscher ein digitales Koordinatenmessgerät mitsamt einer Analysesoftware. Das digitale Messgerät kommuniziert mit zahlreichen maschineninternen und -externen Sensoren, die während des Fräsprozesses Prozessdaten aufnehmen.
Die Analysesoftware des Fraunhofer IPT verarbeitet die Daten mithilfe verschiedener Technologiemodelle weiter: Sie verrechnet beispielsweise die sensorisch erfasste Zerspankraft des Werkzeugs mit den Simulationsdaten zur Steifigkeit der Bauteilgeometrie. Daraus lässt sich die Abdrängung des Werkstücks während der Fräsbearbeitung ermitteln, die einen wichtigen Indikator zur Beurteilung der Qualität der Bauteiloberfläche liefert. Mithilfe dieser und vieler weiterer Daten und Analysen entsteht ein digitaler Zwilling des Bauteils bereits während der Fertigung. Das digitale Messgerät kann damit schon im laufenden Prozess präzise Aussagen über dessen Bauteilgeometrie und Oberflächengüte treffen.
Ergebnisse der Qualitätsvorhersage im Praxistest bestätigt
Zur Überprüfung der DigitalCMM-Technologie fertigte das Forschungsteam am Fraunhofer IPT eine Blade Integrated Disk (Blisk), ein hochkomplexes, sicherheitskritisches Bauteil aus dem Flugzeugantrieb. Das Ergebnis bestätigte den Nutzen des errechneten Digitalen Zwillings: Die Werte der Qualitätsvorhersage und der physischen Messung stimmten mit einer Abweichung von höchstens zehn Mikrometern überein – also mit einer Genauigkeit, die die Forschenden für die Anwendung in hochkomplexen Zerspanprozessen als sehr gut beurteilen. Das digitale Koordinatenmessgerät und die Analysesoftware bieten in Verbindung mit dem Digitalen Zwilling ein effektives Werkzeug, Zeitaufwand und Kosten für nachgelagerte Qualitätsprüfungen gefräster Bauteile zukünftig deutlich zu reduzieren.
Förderung
Das Forschungsprojekt »DigitalCMM – Digital Coordinate Measurement Machine« wurde durch Mittel der Europäischen Union im Programm »EFRE.NRW, Produktion.NRW« gefördert.