Fraunhofer IPT reduces part distortion during milling
Part distortion is a major cost factor in the production of metallic parts, especially in the case of large and thin-walled workpieces that play an important role in lightweight design or in aerospace. The Fraunhofer Institute for Production Technology IPT in Aachen, together with partners, has now successfully developed a system for reducing part distortion caused by residual stresses: With model-based process design and a new type of clamping system, companies will be able to significantly reduce part distortion during milling in the future.
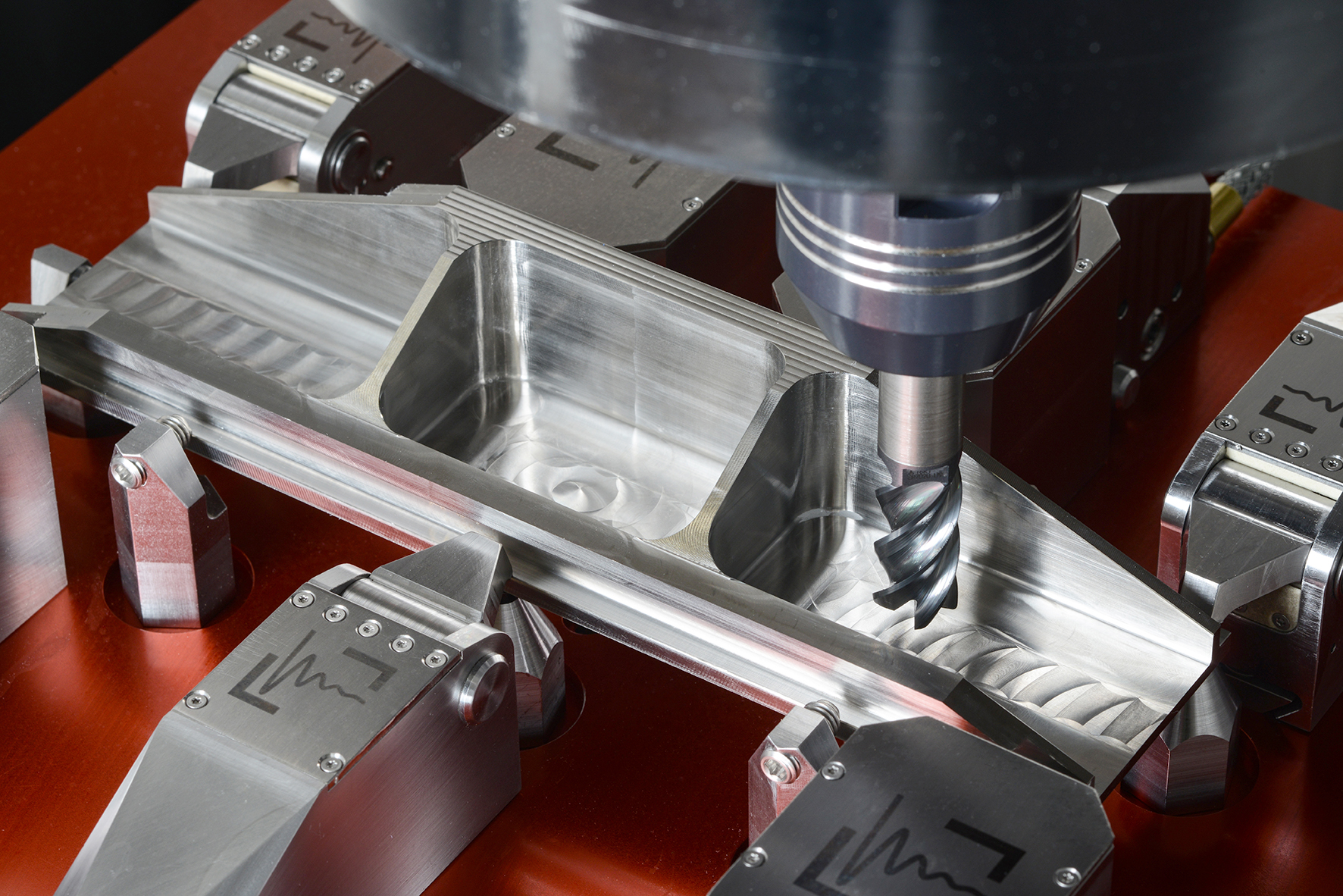
During the production and subsequent heat treatment of metallic blanks, residual stresses are generated which lead to shape and dimensional deviations of the workpiece during machining. Especially after unclamping, when the workpiece is released from the clamping system, significant distortion of the part occurs. Part distortion of this kind means that the manufacturing tolerances cannot be maintained and the part has to be reworked. A 2001 report by aerospace company Boeing estimated the company's annual costs for delay-related rework and scrap at about $290 million.
Finite Cell Method (FCM) for simulating part distortion caused by residual stresses
A team from the Fraunhofer IPT, together with its partners in the "VoKoES" research project, developed a concept consisting of a simulation software and a new type of clamping system that can be used to predict and reduce part distortion during milling of rolled and heat-treated workpieces. Using the example of an aerospace structural component made of the titanium alloy Ti‑6AI‑4V, the project team was able to demonstrate that the solutions developed reduced the distortion by 94 %.
To this end, the researchers and their partner Access e.V. first programmed a thermomechanical FEM-simulation to determine residual stress states in heat-treated blanks. In addition, a numerical distortion simulation was developed, that allows to predict the part distortion after each milling operation.The Fraunhofer IPT researchers programmed the simulation together with the Institute for Structural Mechanics and Lightweight Design (SLA) at RWTH Aachen University based on the Finite Cell Method (FCM).
Successful integration of simulation into CAM system
Together with the project partner Module Works GmbH, the Fraunhofer research team successfully integrated the simulation software into a CAM system for tool path planning. Based on the part distortion prediction, the team tested various compensation methods, such as varying the machining sequence or the position of the target part within the blank. The results of the compensation methods are visualized directly in the CAM system. The integration into the CAM system has the advantage that no additional software is required. Another advantage of the process is that it can basically be applied to all workpiece geometries as well as subtractive manufacturing processes.
Adaptive, hydraulic clamping system for distortion-reduced milling operations
In addition to the digital solutions for predicting and reducing part distortion, project partner Innoclamp GmbH from Aachen, Germany, developed an adaptive, hydraulic clamping system for milling aerospace structural components. With the new clamping system, residual stresses in the clamped workpieces can be released in a controlled manner during machining; the stress-free workpieces are then machined further. In this way, the desired geometries can be produced without part distortion after unclamping. Part distortion between machining steps is thus allowed without losing the part's references and without the need to re-measure the part. The solutions developed were successfully demonstrated in the last project phase using the example of an aerospace structural component made of the titanium alloy Ti-6AI-4V both at the Fraunhofer IPT and at the project partner BoTech GmbH.
Application of the digital twin also for vibration prediction during turning and post-machining of additively manufactured components
The research team plans to expand the simulation software in follow-up projects to include additional physical mechanisms, such as workpiece and tool deflection. In addition, the methodology could also be applied to additive manufacturing processes, because part distortions also frequently occur in additive manufacturing, for which adapted compensation strategies must be developed. Further development of the adaptive clamping system is also already being planned.
Funding
The research project "VoKoES – Prediction and compensation of part distortions due to residual stresses during 5-axis milling" was funded by the European Regional Development Fund (EFRE) 2014-2020.
Project partners
- Fraunhofer Institute for Production Technology IPT, Aachen (coordination)
- Access e. V., Aachen
- RWTH Aachen, Institute of Structural Mechanics and Lightweight Design (SLA)
- Innoclamp GmbH, Aachen
- Module Works GmbH, Aachen
- BoTech GmbH, Mönchengladbach