Formnext 2021: Fraunhofer IPT, FH Aachen and Präwest produce new hydrogen combustion chamber design using 3D printing
Hydrogen is becoming an increasingly important energy carrier against climate change. Although hydrogen combustion does not release any carbon dioxide, what hardly anyone knows is that it produces more nitrogen oxides (NOx) than the combustion of fossil fuels. In a joint research project, FH Aachen – University of Applied Sciences and the Fraunhofer Institute for Production Technology IPT in Aachen, together with Präwest Präzisionswerkstätten GmbH & Co KG in Bremen, have used Additive Manufacturing to produce a hydrogen combustion chamber in a new design that can significantly reduce nitrogen oxide emissions. The partners are now presenting this prototype to the public at Formnext, the trade fair for Additive Manufacturing and industrial 3D printing.
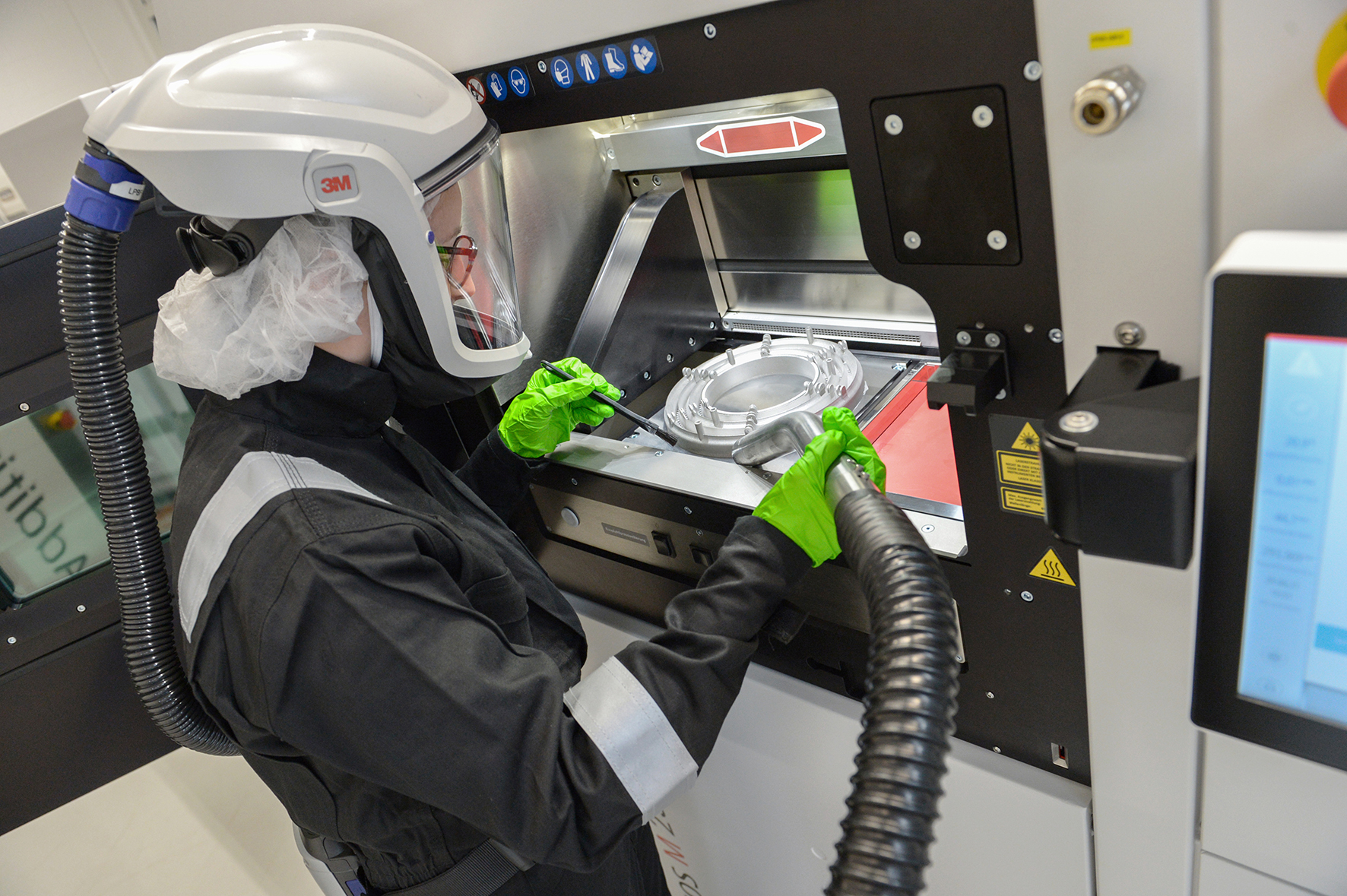
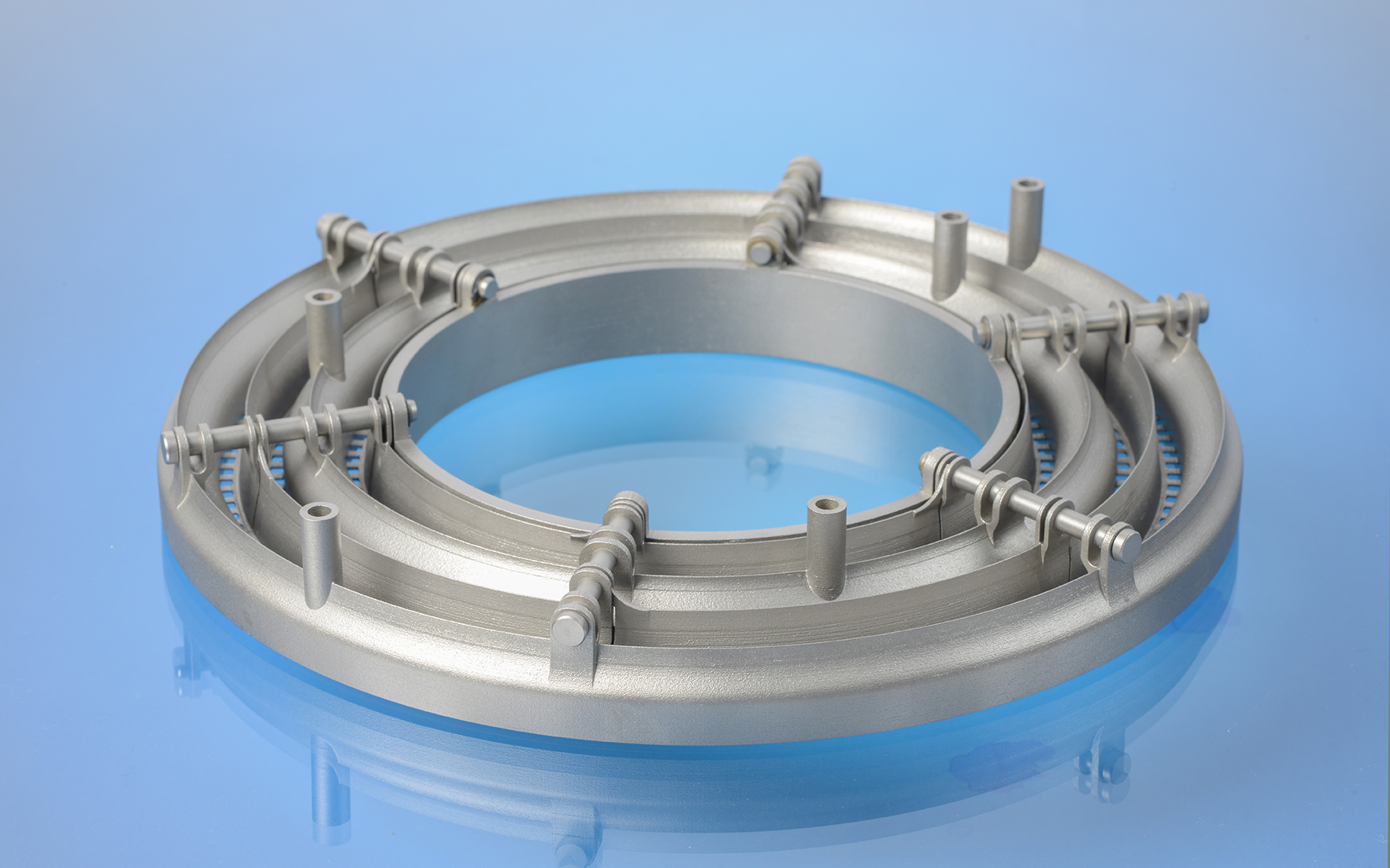
The design of the hydrogen combustion chamber that the partners will be showing at the fair supports the MicroMix combustion process (MMX), developed by Prof. Dr. Harald Funke at the Faculty of Aerospace Engineering at FH Aachen – University of Applied Sciences, which was awarded the FH Aachen Research Prize 2021 in October. This combustion process relies on a large number of smaller flames compared to conventional combustion processes with a few large flames. The MMX combustion chamber is designed in such a way that the gas mixes optimally with the supplied air and burns with less NOx emissions. Another advantage of the small flames in the chamber is the higher safety against flashback, making such combustors in appropriate scaling suitable not only for stationary gas turbines but also for aerospace applications.
However, the production of MMX combustion chambers is technically quite challenging, because the manufacturing tolerances are small: The operation of such a combustion chamber with the volatile hydrogen gas requires that the system remains permanently leak-tight. In addition, all the functional elements inside the chamber, such as the air baffles, must be precisely aligned with each other to ensure the desired flow characteristics of the incoming and outgoing gases. However, manufacturing just by subtractive manufacturing processes such as milling and drilling would make components of this kind very costly. Therefore, the project partners chose an additive process to build their prototype: Laser Powder Bed Fusion (LPBF).
LPBF: Metallic 3D printing for complex components
LPBF is a well-known Additive Manufacturing process that can be used to build up the combustion chamber from a metal powder. This involves a micro-welding process in a powder bed to melt the cross-sectional area of the component layer by layer. Extremely thin layers make it possible to produce the complex component geometry in a high resolution, with many functional elements already created inside the combustion chamber. This significantly reduces the amount of finishing operations required.
After printing the combustion chamber and the separation of the platform on which it was built, only a few subtractive post-processing steps by milling and drilling are required: For example, the filigree, movable air baffles are manufactured in a milling process and the holes for the hydrogen outlet are added subsequently. By combining the individual manufacturing steps, the three partners are able to compensate for the weaknesses of the existing manufacturing processes and to link them into a synergetic process chain.
Additive design of the MMX combustion chamber promises cost savings of up to 90 percent in production
The MMX concept has already proven itself in test operation. Based on simulations, the Aachen researchers also predict that the use of LPBF can significantly reduce the time required for assembly and cut the costs of such a combustion chamber by up to
90 percent. In addition to the ecological and economic advantages that the new combustor technology offers anyway, LPBF also makes the manufacturing processes more sustainable and requires a lower use of resources than conventional production from individual components that must be assembled at great expense and with comparatively high material consumption.
A first functional prototype of the MMX combustion chamber as well as various other components produced with Laser Powder Bed Fusion and by "Express Wire Coil Cladding (EW2C)", a new wire-based Laser Metal Deposition process, will be exhibited by the Fraunhofer IPT from November 16 to 19 at Formnext in Frankfurt at the joint booth of the Fraunhofer-Gesellschaft in Hall 12, Booth D41.
Project partners
- Fraunhofer Institute for Production Technology IPT, Aachen
- FH Aachen - University of Applied Sciences, Aachen
- Präwest Präzisionswerkstätten Dr.-Ing. Heinz-Rudolf Jung GmbH & Co. KG, Bremen
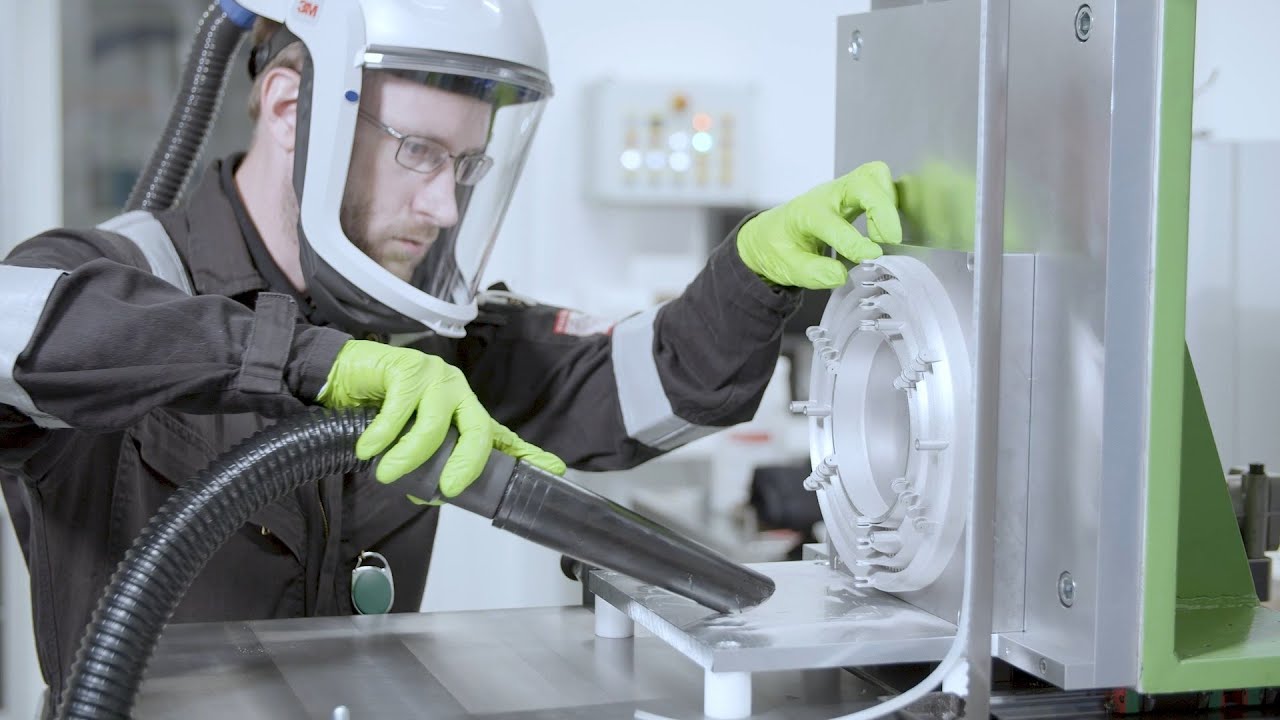