Formnext 2023
Well thought-out and tested from start to finish: production chains for additive manufacturing
Over the past eight years, since Formnext opened its doors as a trade fair for additive manufacturing, the market and the needs of the industry have changed significantly: Whereas in the beginning, sheer enthusiasm about the technical possibilities dominated, companies now demand flawlessly functioning solutions for processes and systems technology in order to turn new ideas into concrete products quickly and cost-effectively. This year at the trade fair, the Fraunhofer Institute for Production Technology IPT from Aachen will be demonstrating how it ensures that production chains function seamlessly and what is required to turn a 3D-printed object into a finished end product.
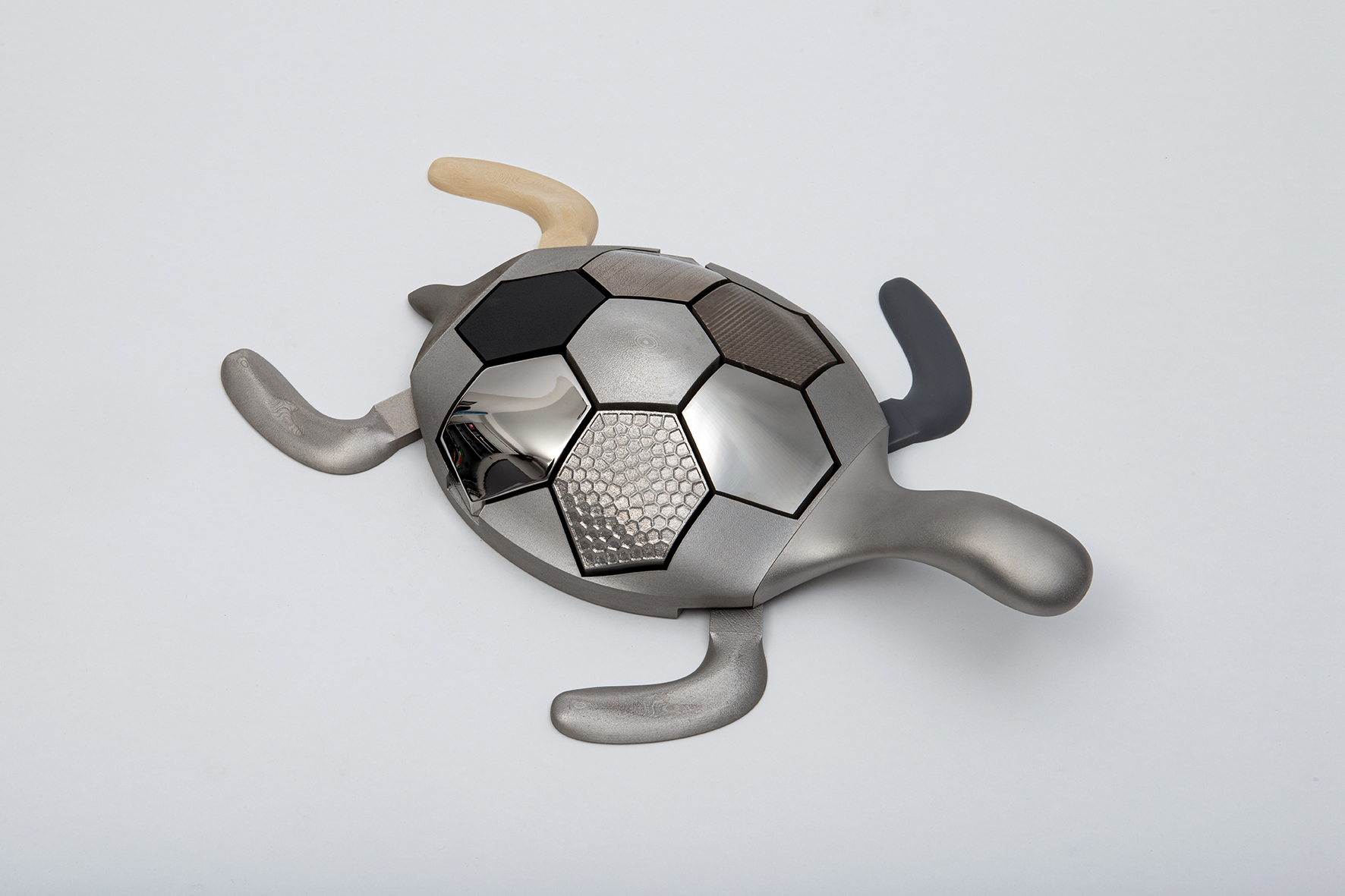
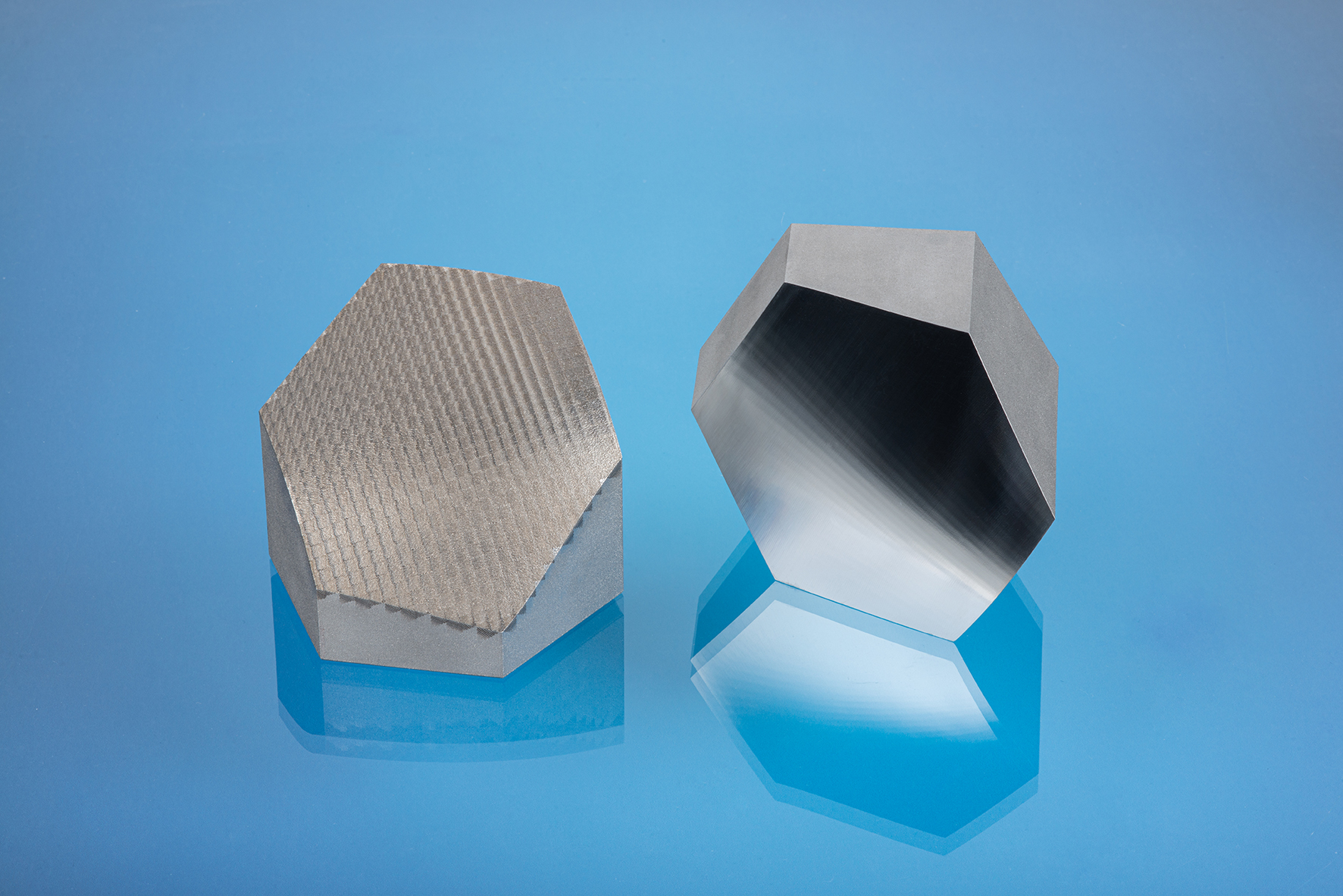
Metallic 3D printing from a powder bed is generally regarded as a prototype for additive processes, as additive construction using lasers allows enormous design freedom while using materials sparingly. However, on closer inspection, many companies realize that the finished product or component is a long way from being ready after printing. Extensive reworking is often required to achieve the desired shape accuracy, remove support structures or add design elements.
Additive and subtractive manufacturing – from "semi-finished product" to ready-to-use component
"Basically, the additively manufactured part is not yet a component, but rather a semi-finished product," explains Robin Day, who heads the directed energy manufacturing department at Fraunhofer IPT. At the institute, he plays a leading role in developing the entire production chain so that additive processes and post-processing from a single source lead to a flawless and ready-to-use component. The research work in this area, therefore, does not focus solely on testing and assessing the individual processes and their interlinking in advance and calculating the costs: "We use our own machines and systems to directly test what we have come up with on paper and on the computer using suitable demonstrator components. We do this because only when the production steps are actually interlinked do stumbling blocks become apparent, which we then specifically eliminate," says Robin Day.
Thanks to the institute's extensive technical infrastructure, the scientists in its department are able to run through the process chains and combinations of different additive and subtractive processes in-house from start to finish and remove physical obstacles. In combination the weaknesses of the respective processes can also be compensated for and the time and costs required for series production can be significantly reduced. For this reason, the current field of research not only includes powder bed processes, but also, for example, the deposition welding of wire with laser and electric arc – in various combinations with ablative technologies, from milling, turning or grinding to structuring with the laser.
From small structures to very large: multi-technology platform as an example of flexible and sustainable process chains
One of Fraunhofer IPT's aims is to work with industry in research and development projects to develop adaptive and efficient manufacturing processes and process chains that can be integrated into existing production environments at the lowest possible cost. To this end, the institute has now integrated various processing heads for laser structuring as well as laser and arc cladding into a standard industrial robot. This equipment allows even large metal components to be processed quickly, precisely and cost-effectively in a single clamping operation. By simply changing the processing heads, the Aachen scientists can combine additive and ablative processes in a comparatively cost-effective overall system.
Process diversity and process combinations at the stand: compact overview at Formnext
At Formnext 2023, the Fraunhofer IPT and twelve other Fraunhofer Institutes will be showcasing examples of numerous processes and their combinations: conventional processes for smoothing surfaces such as milling and sandblasting, but also mass finishing, stream finishing, plasma processes, laser structuring, selective coating and painting. The institutes' joint booth in hall 11.0, Stand D3, offers trade fair visitors a compact overview of different technologies and invites them to discuss their specific challenges.
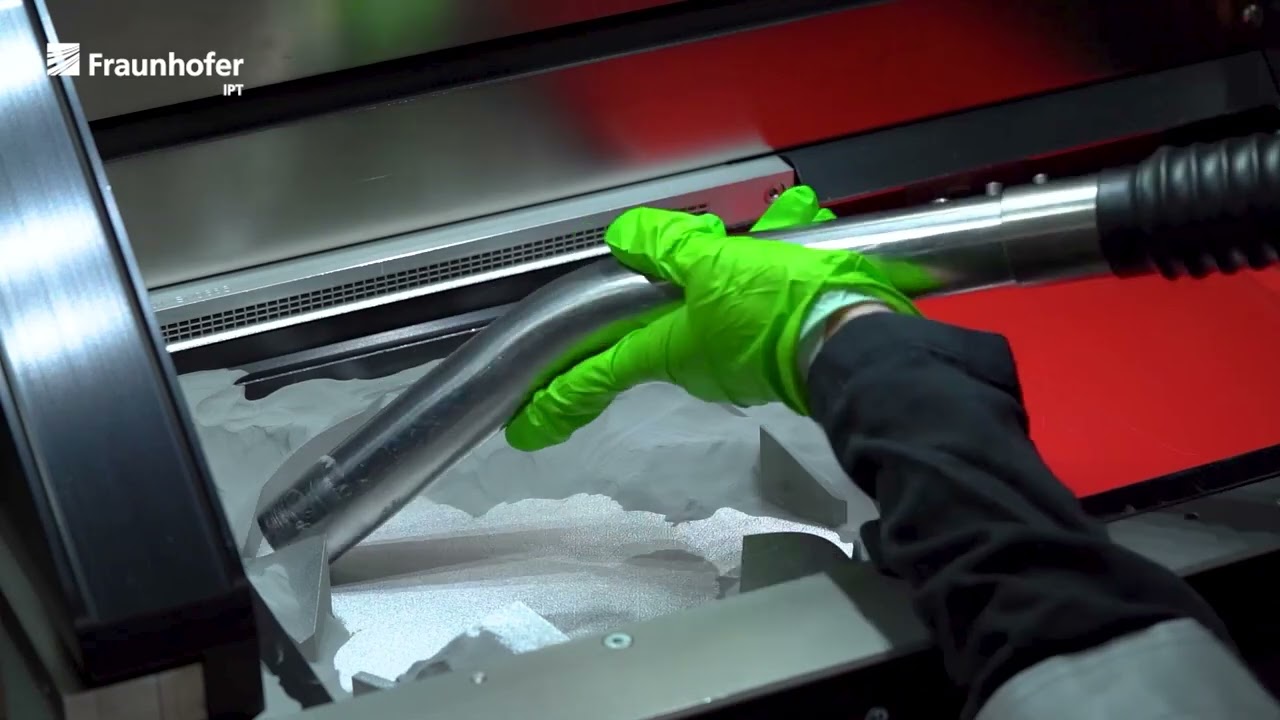
Privacy warning
With the click on the play button an external video from www.youtube.com is loaded and started. Your data is possible transferred and stored to third party. Do not start the video if you disagree. Find more about the youtube privacy statement under the following link: https://policies.google.com/privacyDas Pulverbettbasierte Laserstrahlschmelzen gehört zu den bekanntesten additiven Fertigungsverfahren. Beim LPBF-Verfahren werden die Bauteile durch selektives Laserstrahlschmelzen hergestellt.
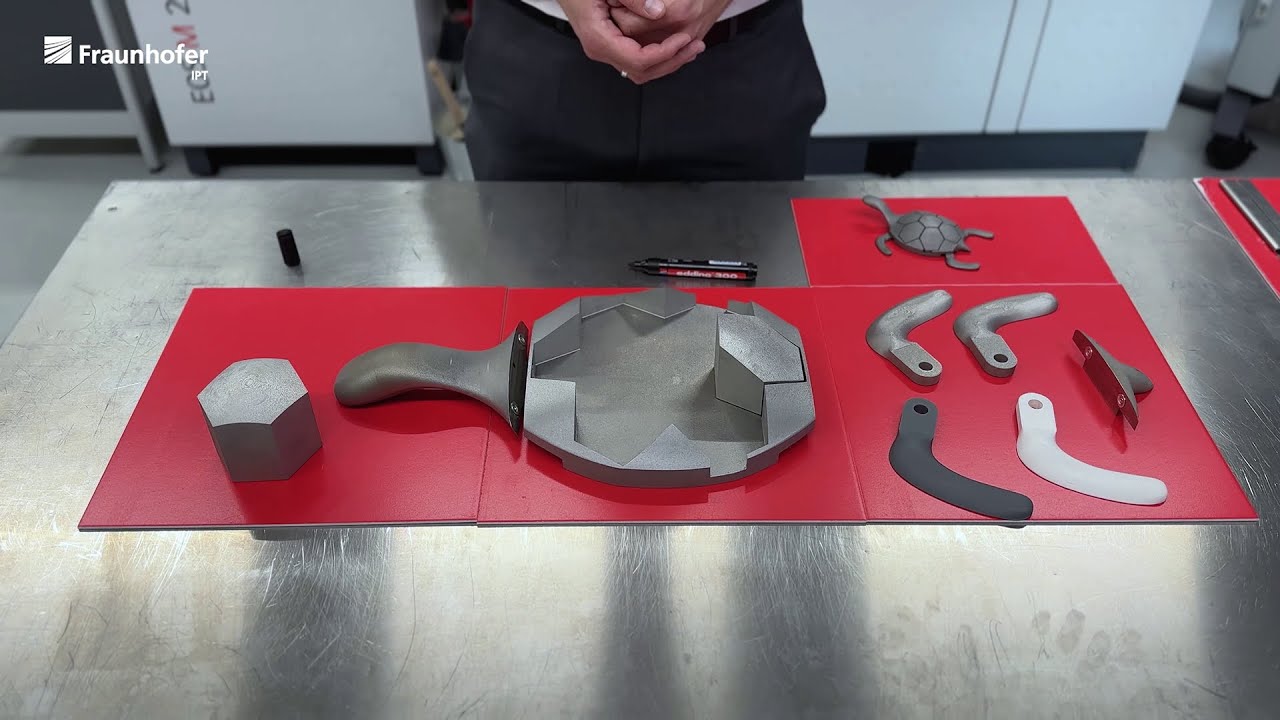
Privacy warning
With the click on the play button an external video from www.youtube.com is loaded and started. Your data is possible transferred and stored to third party. Do not start the video if you disagree. Find more about the youtube privacy statement under the following link: https://policies.google.com/privacyWie wird aus einem additiv gefertigten Halbzeug ein hochwertiges Bauteil für den industriellen Einsatz? Additive Verfahren wie das Laser Powder Bed Fusion (LPBF) bieten hohe Flexibilität und Ressourceneffizienz in der Einzel- und Kleinserienfertigung. Dr. Robin Day, Leiter der Abteilung »Energietische Strahlverfahren« stellt in dem Video einige Nachbearbeitungsverfahren vor.